在工业设备运行中,振动与温度是反映机械健康状态的核心指标。
VRT-2T振动温度变送器通过集成高精度加速度传感器与热敏电阻,实现振动烈度与表面温度的同步监测,结合边缘计算与无线通信技术,为风机、电机、泵类设备提供实时状态感知与故障预警,助力企业实现从“被动抢修”到“主动预防”的运维模式升级。
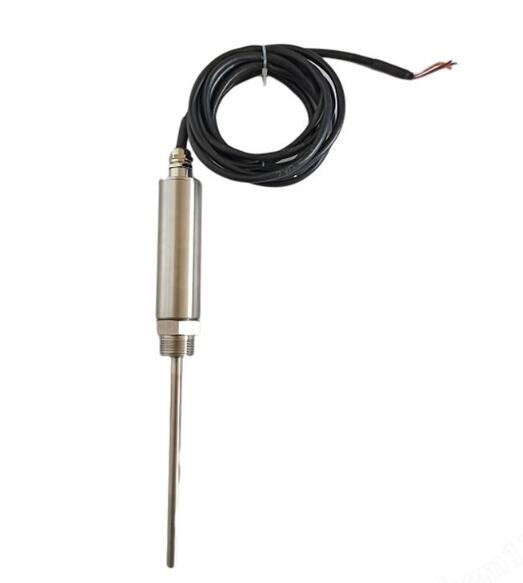
一、技术架构:双参数融合与智能分析
1.多物理场感知模块
VRT-2T内置三轴MEMS加速度计(量程±50g,分辨率0.001g)与PT1000铂电阻温度传感器,可同步采集设备振动速度(mm/s)、加速度(g)及表面温度(℃)。例如,在电机轴承监测中,振动阈值设为7.1mm/s(ISO 10816-3标准),温度阈值设为85℃(基于轴承寿命曲线),实现双重保护。
2.边缘计算与动态预警
设备搭载ARM Cortex-M7处理器,支持实时FFT频谱分析(频率分辨率0.1Hz)与温度趋势建模。通过内置的专家知识库,可自动识别典型故障特征,如轴承外圈故障(特征频率1×BPF±10%)、齿轮断齿(啮合频率及其倍频突增)及温度异常爬升(速率>2℃/min)。某水泥厂应用后,因提前72小时预警磨机轴承故障,避免了一次非计划停机。
3.无线通信与云端协同
支持LoRaWAN/NB-IoT双模通信,数据可上传至企业私有云或公有云平台。云端AI模型通过多参数关联分析(如振动与温度的相位差),进一步挖掘设备劣化规律。例如,当振动RMS值与温度同步上升时,系统可判定为润滑失效而非单纯过载,提升诊断准确率至95%以上。
二、部署与应用:从安装到决策支持
1.快速安装与参数配置
采用磁吸式或螺纹固定方式,5分钟内完成设备部署。通过NFC或蓝牙配置额定转速、传感器灵敏度及预警阈值。例如,在冷却塔风机监测中,设置转速300rpm、振动预警值4.5mm/s、温度预警值70℃,并关联至运维人员手机APP。
2.实时监测与故障溯源
设备界面显示振动时域波形、频谱图及温度曲线,支持历史数据回放。某石化企业通过分析泵体振动频谱(发现2×叶轮通过频率突增),结合温度异常点定位,精准判断为叶轮气蚀问题,指导更换叶轮材质,延长设备寿命2倍。
3.维护决策与成本优化
系统自动生成设备健康报告,包含MTBF预测、备件需求清单及维修优先级排序。某汽车工厂应用后,设备平均维修时间缩短40%,年维护成本降低30%。
三、行业价值与未来趋势
VRT-2T振动温度变送器已广泛应用于风电、冶金、化工等领域。在某风电场,通过监测齿轮箱振动与轴承温度,结合SCADA数据,成功将齿轮箱故障预测准确率提升至88%;在半导体工厂,对洁净室风机实施双参数监控,确保环境参数波动<5%,保障产品良率。
未来,VRT-2T振动温度变送器将向多参数融合(如增加电流、压力监测)、微型化(体积缩小50%)及自供电(能量采集技术)方向发展,进一步降低部署成本,推动工业设备智能化监测的普及。作为工业物联网的关键节点,VRT-2T正以双参数感知与智能分析能力,重新定义设备健康管理的边界。